Products/Solutions
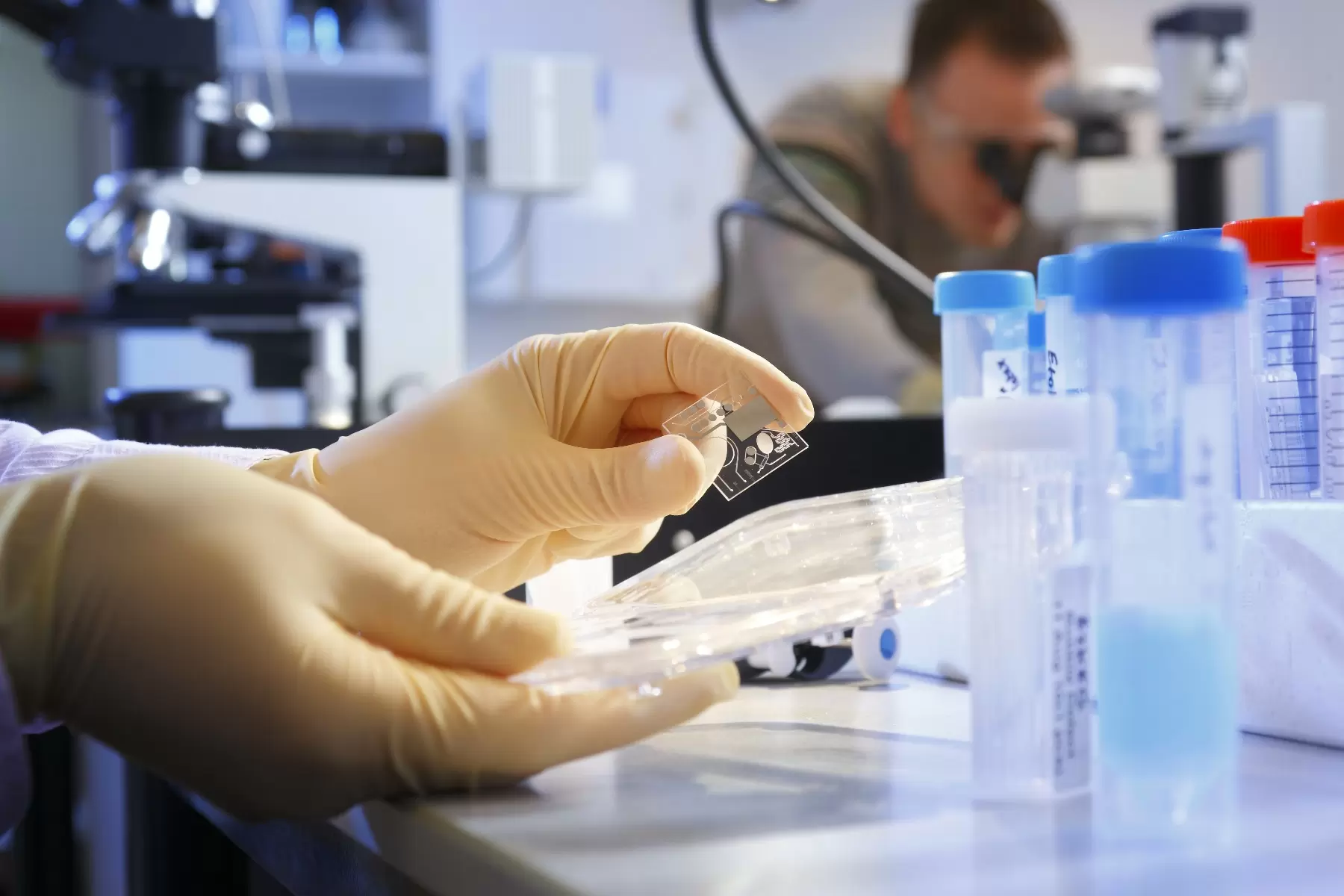
Micronit Success Story
Who are you and what does MICRONIT do?
My name is Tony Ekkelenkamp and I work at Micronit as a Quality Assurance Program Manager. Micronit is located in Netherlands and it focuses on contract development and engineering and contract manufacturing of microfluidic components. Our customers are located in a wide range of industries such as aerospace technology, invitro diagnostics or medical devices and also Pharmaceutical industry. Our products are mainly used in life science applications or point of care diagnostics and drug delivery, but also space telescopes. So we have a very wide array of customers, but most of them are located in medical applications. We are ISO 13485 certified and we also try to comply with other standards that our customers require. My responsibilities include managing the improvements of our quality management system and alignment of our policies with updated regulations.
What challenges were you facing before implementing BPAMedical365?
Before we started actually digitalizing all our system into a single environment, we were having multiple systems in multiple environments. And that ranged from document management to management of CAPAs, nonconformities, complaints, changes. So we struggled with maintaining several systems at the same time and therefore we searched for a possibility to integrate all those elements of out quality management system into a single environment. Another point is that from a medical device perspective and pharmaceutical perspective, there were more requests for signature validations which did not meet the required standards at that moment. And we searched for a solution that did meet those requirements.
Why did you choose to go for BPA Solutions?
One of the requirements we were looking for is that it could be integrated into our Microsoft 365 environment and we could also integrate it with other systems such as our ERP system. Because BPA runs on the Microsoft 365 environment, it was a really nice fit. Of course, we looked at the price and BPA offers a competitive price compared to other eQMS suppliers, which also provide a whole packaged solution. Also, BPA offers some standardized workflows that can be modified to fit your needs. You can also design your own workflows and modify your own processes.
Which solution and module have you implemented?
So we did implement BPA Medical with compliance documents, non-conformities and competence management.
Which result were you able to achieve with the BPA’s software?
Performance is one thing. For example, we are a contracting organization and we get audited a lot by our customers. What we saw is that those audits are much smoother because we can find documents more easily. We can find records more easily. Providing a report, for instance, a non-conformity is much more clear to the customer. And also another point is we are now able to keep an eye on current trends within our system and that also makes the management of the system much more effective.
BPA solutions actually provides a platform where you can actually create overviews of data. Components such as E signatures and standardized workflows do provide you some guidance to how to actually arrange your quality management. BPA Solutions give you more guidance on what to do and how to do things more effectively and how to design your process
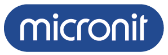
Manufacturing
Medical Devices
Pharmaceutical